Technology Title
Digital Twin Companion Tool
Tech Focus Area
Aircraft Data Integration
Abstract
Most DoD structures are designed using damage-tolerant principles, therefore are subject to periodic manual inspections and preventative care based on assumed usage profiles. These profiles are conservative, impacting asset availability, but also cannot anticipate every combination of conditions, further affecting availability with unplanned maintenance. Digital twins can be an effective tool for greatly improving maintenance logistics—predicting health-state of individual assets based on actual usage and exposures—but these models are only as accurate as the fidelity of their inputs. The key to unlocking the potential benefits of digital twins is getting the right data from the right sensors in the right places. The challenge that exists is installing many sensors on an asset also means many separate cables, acquisitions systems and software interfaces.
Metis Design Corporation (MDC) in collaboration with Analog Devices Inc (ADI) have developed a Digital Twin Companion (DTC) Tool, which is ultra-low-power distributed system-on-chip (SoC) sensor infrastructure to facilitate meaningful digital twin predictions. This ruggedized hardware (10x10x3 mm, 1 gram) accepts a wide range of off-the-shelf analog and digital sensors, is compatible with specialized piezoelectric transducers and crack and corrosivity gauges and has on-board algorithm processing capabilities including resources for machine learning. Rather than patching standalone systems for each type of sensor, the DTC tool serves as a common backbone to accumulate data from all on-board sensors. The distributed approach allows for a digital bus, meaning units can be daisy-chained on a single cable and plug-and-play, yielding nearly unlimited scalability and versatility. At the end of the bus a tiny DTC base provides flexible power and data interfaces, including operating off 3-48VDC batteries or vehicle power, and on-demand, triggered logging and continuous streaming data modes.
Graphic
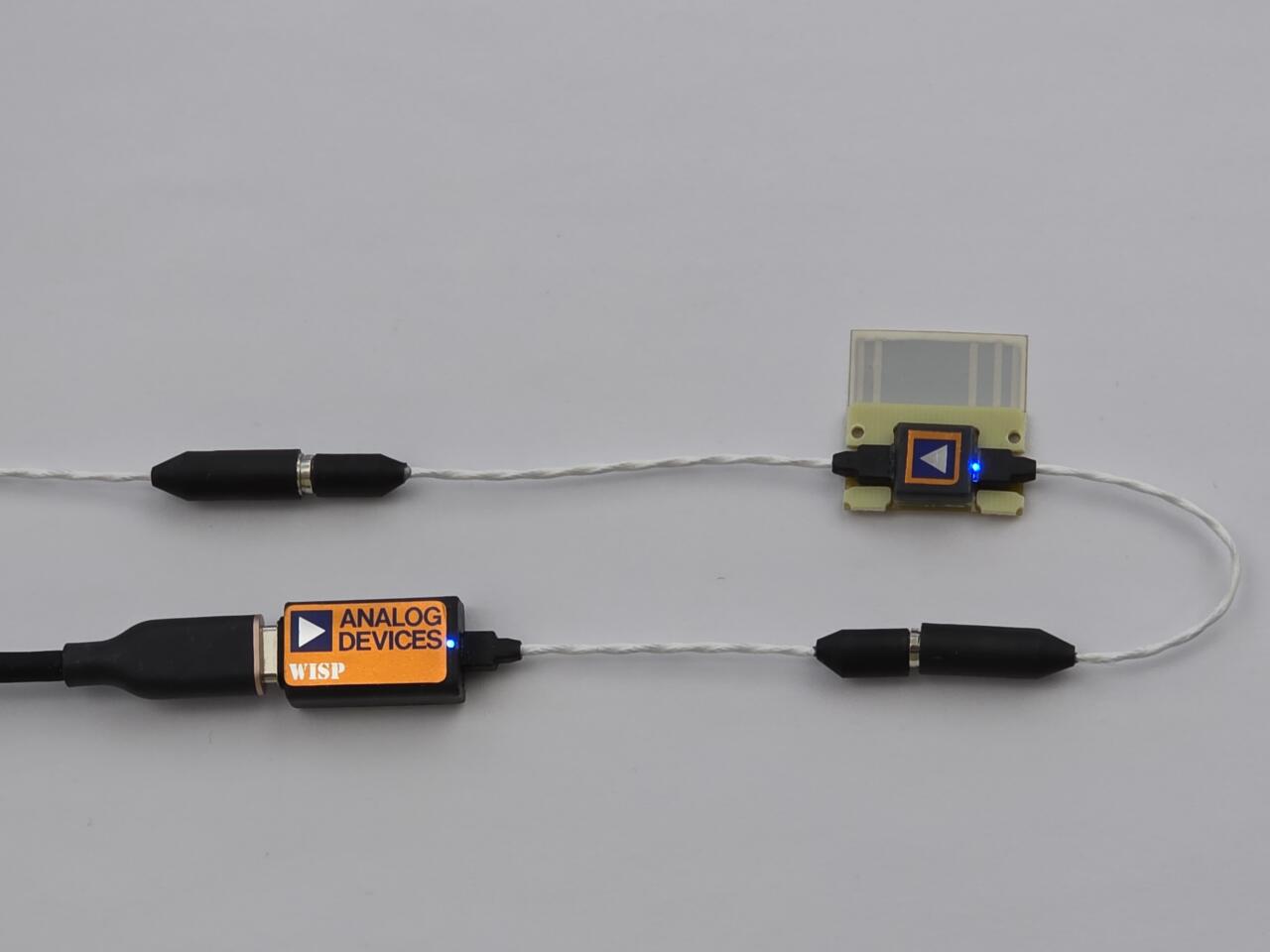
This system has been test flown on a USAF F-15, participated in sea trials on a USN destroyer, and soon will launch into space as part of a USSF mission. TRL7 has been achieved through in-service measurement of temperature, pressure, humidity, crack growth and corrosivity. Implementing the DTC tool on DoD assets will enable a convenient mechanism to obtain the quality and quantity of data necessary to properly fuel digital twins for condition-based maintenance (CBM). CBM will allow maintainers to plan more efficiently, improve logistics for repairs and replacement components, minimize downtime and maximize readiness. Safety would also be improved by providing a means to capture unanticipated failure modes. This technology would be applicable to nearly any DoD asset, ranging from vehicles to bridges to aircraft hangers.
MDC is presently working with the F-15 SPO, AFRL and ASIP towards the first successful transition of this technology to the F-15 fleet to inform decision making between planned depot maintenance (PDM).