Precision Additive Solutions, Inc. is advancing the Laser Powder Bed Fusion (LPBF) ecosystem with the first platform engineered specifically for the safe, repeatable, and high-quality production of aerospace-grade parts at scale. Our system is built to process reactive alloys (magnesium, aluminum, titanium), non-reactive alloys (Inconel, copper), and refractory metals (tungsten, molybdenum, cobalt) with precision, consistency, and industrial throughput.
We integrate three core innovations that set us apart:
Selective Stepped Laser Melting (SSLM™) – A proprietary process for adaptive melt control that enhances material integrity.
Specialized Architecture for Reactive Material Handling – Enabling safe and efficient processing of challenging alloys.
Precision Additive Qualification – A rigorous methodology that ensures repeatability and part certification for aerospace and defense.
Our founder brings over two decades of experience in additive manufacturing, casting, and aerospace engineering. His patented technologies have supported national security and aerospace missions, including India’s Moon and Mars programs with ISRO.
Focus Area: Advanced/Additive Manufacturing
Contact
Mike Simek
mike.simek@precisionadditive.com
317-319-3953
3D+™ Hybrid Printing Technology
Problem Statement:
Aerospace and defense platforms depend on lightweight, high-performance materials, but the U.S. industrial base is no longer equipped to meet growing demand using traditional manufacturing methods. The supply chain for critical components has eroded due to domestic facility closures, reliance on foreign sources, and extended lead times. Meanwhile, additive manufacturing—particularly laser powder bed fusion (LPBF)—has not yet matured into a scalable, certifiable solution for standard aerospace metals such as aluminum and titanium.
Today’s production landscape faces four critical barriers:
- Diminishing Domestic Manufacturing Sources
- Raw Material Shortages and Extended Lead Times
- Material and Process Complexity
- Limited Scalability
Technology Solution Statement:
Our 3D+™ hybrid printing technology (currently in development) sets us apart. This integrates reactive and refractory material processing, in-situ quality monitoring, real-time adaptive print parameter adjustment capability, in-process machining, small, medium, and large-scale Laser Powder Bed Fusion (up to 1.2m x 1.2m x 1.2m build volume), and a new, high-speed, extremely low spatter laser printing technology in Selective Stepped Laser Melting (SSLM™). SSLM™ provides position-by-position melt pool control through dynamically adjusted colinear beam parameters. It enables spatial variation in energy delivery, adaptive focus diameter control, and real-time thermal regulation. These capabilities predict and minimize porosity, suppress spatter, and allow for both high-fidelity feature resolution and high-rate deposition. This results in exceptionally high-quality finished parts, and a digital twin of the entire build process.
To address throughput, stabilize production, improve safety, and minimize operator touch times throughout the part manufacturing life cycle, PA systems integrate the necessary post-processing steps as part of the printer and factory design, including automated de-powdering, stress relief, and heat treatment. Our machines are further optimized to match the needs of each material, allowing PA to specialize in printing reactive (e.g. magnesium, titanium, aluminum) and refractory (e.g. molybdenum, cobalt, tungsten) alloys.
Benefits Statement:
Precision Additive addresses enabling true viability for alloys already in use, and pioneering pathways for materials previously inaccessible to additive manufacturing. We have developed a holistic qualification strategy that reduces reliance on coupon testing and instead emphasizes robust process controls, in-situ monitoring, and quality assurance integrated into the machine design. In practice, this approach means strengthening QMS certifications, ensuring regulatory compliance, establishing material traceability, machine-specific baselining, statistical process control, qualifying final part performance, and fortifying data management and cybersecurity.
By shifting from labor-intensive coupon testing with limited process knowledge to advanced process monitoring and strict process discipline for informed testing, we can accelerate deployment, reduce costs, and deliver greater confidence in flight-critical AM components.
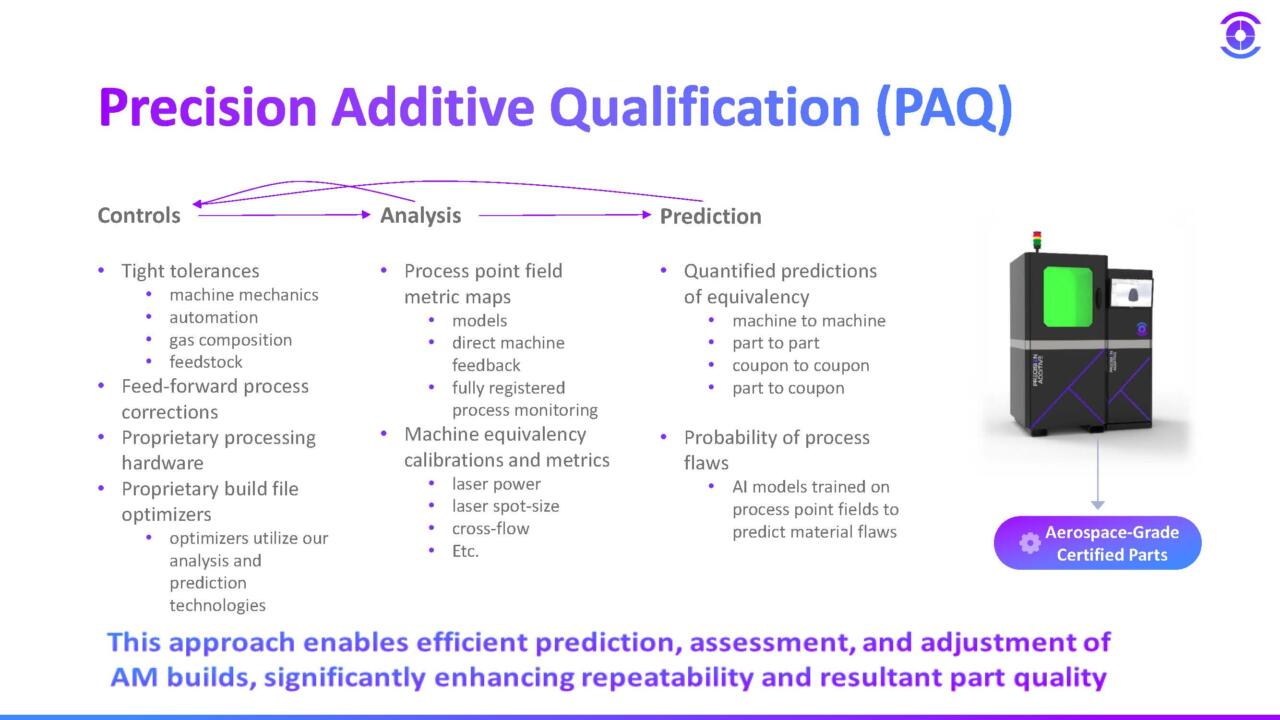