Naval Systems, Inc. (NSI) was founded in 2004 as an technical services company with the Navy’s Naval Air Systems Command (NAVAIR) as its primary customer. Since then, NSI has grown to over 300 employees and some 200 subcontractors, with its headquarters near NAS Patuxent River, MD, and personnel and satellite offices located across the U.S. and overseas. NSI supports USN, USMC, USAF, and US Army programs and associated Department of Defense (DoD) agencies responsible for delivering and sustaining advanced defense systems across warfighting domains.
NSI’s Score Technology and Analytics Center (STAC) empowers warfighters with superior analytics and business solutions. These efforts support the Naval Aviation Enterprise (NAE) with Big Data Analytics leveraging data from operational, maintenance and supply systems to provide key measures to decision makers.
NSI performs systems integration on multiple unmanned/autonomous systems out of its ISO 9001/AS9110 Panama City, Florida Product Integration Facility (PIF) and performs repair and rework as well as supply chain management activities out of its 60,000 SF ISO 9001/AS9120 facility in Jacksonville, Florida. These efforts are complemented by NSI’s core capabilities in logistics/integrated product support, maintenance planning and analysis, supply chain digital tool development, FMS case development and sustainment, and international airworthiness.
Focus Area: Business IT and Analytics
Contact
Ed Nork
enork@n-s-i.us
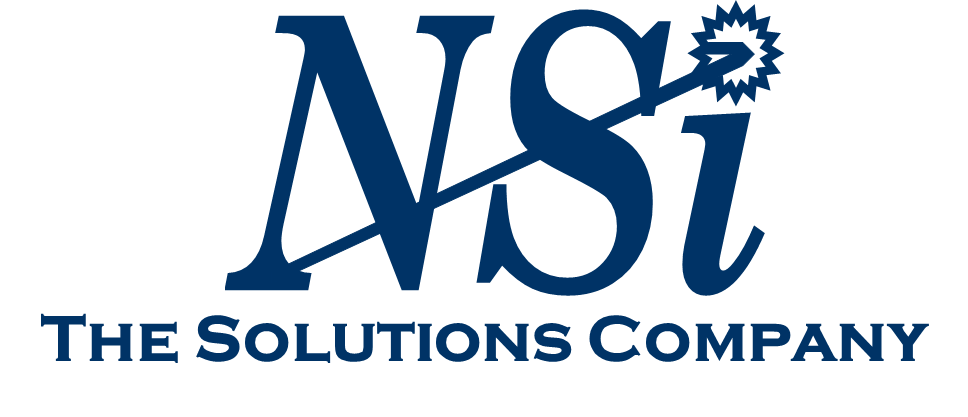
Application of Commercial Off-The-Shelf (COTS) FARO Quantum Laser ScanArm (FQLS)
Problem Statement:
- The current Navy-maintained Aerial Refueling Stores (ARS) are over 20 years old and many components are no longer manufactured.
- Corrosion on mission-critical assets often remains undetected until severe damage occurs.
- Traditional inspections lack continuous, actionable data, hindering maintenance prioritization.
- This gap increases unexpected downtime, repair costs, and reduces overall readiness.
- Defect detection is inconsistent, causing delayed repairs, increased costs, and reduced operational readiness across critical assets.
- Incomplete or inaccurate corrosion documentation limits root cause analysis and impedes long-term maintenance planning.
Technology Solution Statement:
- The FQLS enables rapid reverse engineering and reconfiguration of ARS pods by capturing components for redesign
- Supports full structural and material assessments to modernize a 20+ year-old system
- Identifies imperfections during MRO using 3D scanning, digital reproduction, and CAD
- Enhances durability, efficiency, and adaptability through precise analysis and redesign of ARS components
- Analytics- FQLS identifies hidden corrosion patterns and predicts high-risk areas, solving the challenge of unpredictable asset failures and enabling timely, targeted maintenance to prevent costly downtime.
Benefits Statement:
- An upgraded ARS and its components result in increased readiness, greater decision advantage, decreased risk, and cost optimization due to upfront resolution of structural and material issues.
- Quality control and safety go hand in hand as the ARS is revitalized and NSI provides solutions for engineering gaps and damaged or ineffective components.
- Increased reliability of the ARS, as well as upfront precise and comprehensive understanding of all actionable insights and solutions across varying levels of urgency.