Entry Requirements
Submissions for the CTMA Technology Competition should include:
- An abstract that explains the technology, its current development status, test/simulation data supporting performance claims, and next steps for its development (500 words maximum)
- Focus Area
- Problem Statement
- Description of the Innovation Solution
- Benefits to the DOD
- Innovation Challenges
- Technical Maturity/Demonstration Results
- A high-resolution format (300 dpi) graphic of your technology. Multiple graphics must be sent as one image.
- A video demonstration of your technology in action.
- This is not a sales pitch, the judges want to see what your technology can do.
- The video should be no longer than 3 minutes.
All submitted content must be reviewed and approved for public release.
Finally, all submissions will be published online and in print. By submitting, you are authorizing release to the public and that the submission has been vetted for public viewing and does not contain proprietary or confidential information.
Focus Area Descriptions
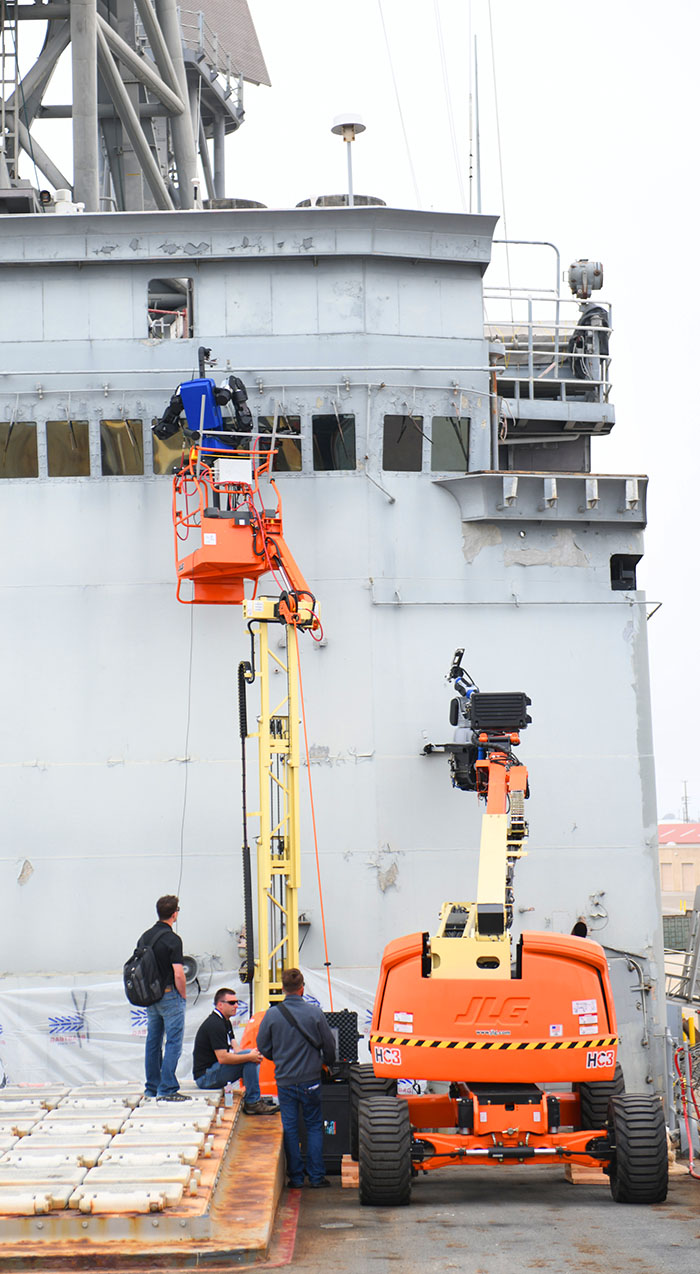