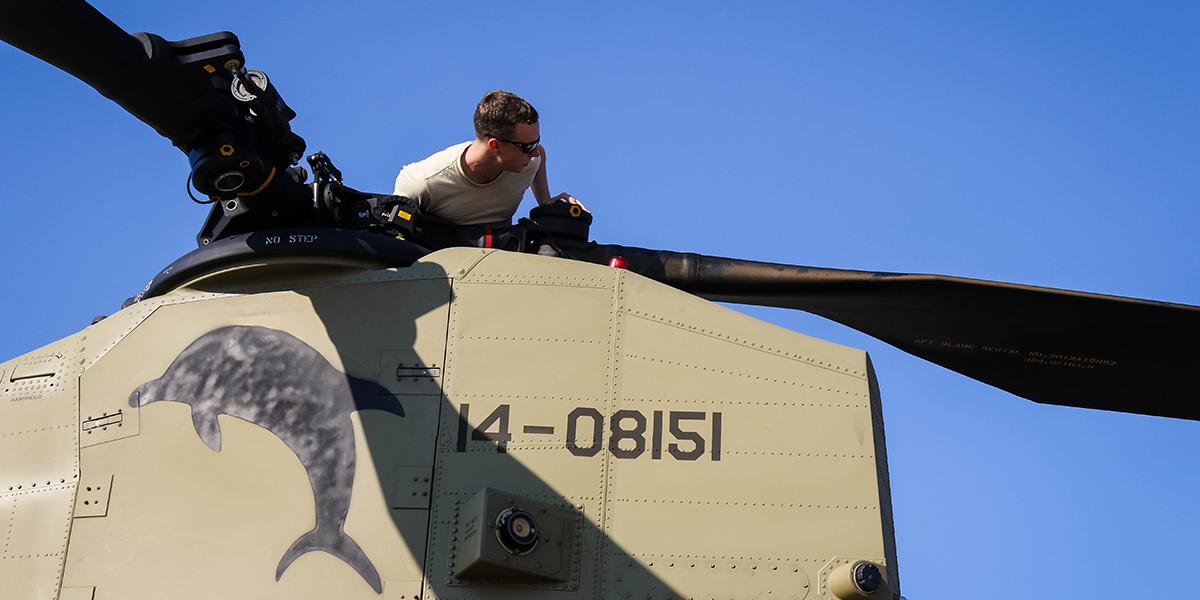
Maintenance professionals who work to sustain the DOD’s fleet of over 5,000 helicopters experience a common challenge with helicopters, especially those operating in desert environments: sand and dust quickly erode rotor blades. Maintaining rotor blades is costly, up to $220,000 for a single UH-60 (Black Hawk) helicopter rotor blade and even more for a CH-47 (Chinook) rotor blade. Protective erosion guards of various kinds have been developed and tested, and the highest-performing ones are manufactured using cold spray. To date, this manufacturing has been done at a prototype level using standard cold spray booths with commercial off-the-shelf robot arms. However, mass-manufacturing the guards requires a dedicated manufacturing process, developed specifically for that task.
A current CTMA project has created a Cold Spray Additive Manufacturing (CSAM) technology that produces erosion guards for rotor blades that extend up to 10 feet in length. The Army Research Laboratory (ARL) is leading the project and collaborating with four industry partners: VRC Metal Systems, Siemens Energy, Solvus Global, and Boeing.
“In this project, we’ve had different types of expertise coming together to solve an important technical problem,” said Marius Ellingsen, Ph.D., Process Engineering Manager – Cold Spray, VRC Metal Systems.
“What’s really unique about this project is we’re making erosion guards, via cold spray, that will have a much longer life, and better performance, than the current erosion guards,” said Brad Richards, Co-founder & CEO, Powders on Demand, a division of Solvus Global.
The CTMA project team took the existing GEN IV® High-Pressure Cold Spray System, manufactured by VRC Metal Systems, and added a new and improved helium recovery system. The GEN IV® system uses helium as a process gas, which creates excellent deposits of the cold spray on surfaces; however, helium is very expensive and there are disruptions in the market.
“To mitigate that we have a helium recovery system that captures the helium that has been used for the deposit,” said Ellingsen. “In this project, we upgraded the recovery system we had in place before. With the upgrades that we performed under this CTMA project, we installed a pressure swing absorption system, which is excellent for getting rid of air and other impurities when you have a gas that’s
fairly well concentrated. The pressure swing absorption system can achieve an incredibly high purity level relatively quickly; we’re talking 99.9 percent or better. Helium is being captured on an ongoing basis, purified, and put into storage so that we can use it again. We can get something like 90 percent of the helium back.”
The CTMA project team integrated VRC Metals’ GEN IV® High-Pressure Cold Spray System, along with the new and improved helium recovery system, into a large robotics system created by Siemens Energy.
“The Siemens Energy team designed and built a highly specialized booth with robotics and advanced controls,” said Ellingsen. “We’re putting VRC Metals’ GEN IV® system inside the booth and hooking it up to a helium recovery system so that we can do these sprays with the best process gas in an economical fashion.”
The integration of the systems created by VRC Metals and Siemens will also improve the precision of using cold spray to produce rotor blade erosion guards.
“We built a robotics system that moves the cold spray applicator along a 10-foot span that follows the curvature of rotor blades,” said Joshua DeAscanis, Program Manager, Siemens Energy. “This is a highly accurate system that enables spraying onto components with extremely complex geometries that were previously difficult to spray.”
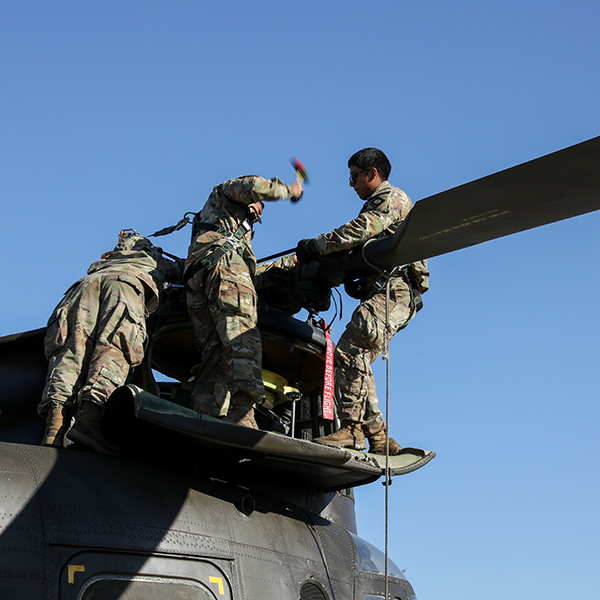
For the material needed to operate the cold spray machine—Niobium powder—Solvus Global secured a domestic supplier.
“Of course, right now there is huge motivation for anything and everything really, especially with respect to critical weapons platforms, to be produced as domestically as conceivably possible,” said Richards.
“The domestic supplier of the powder has been a huge achievement of this project,” said Carlee Schmidt, Senior Materials Engineer, Solvus Global.
The Solvus Global team also focused on ensuring that the domestic supplier can produce enough of the Niobium powder to be able to feed the system as it moves into higher levels of technology maturity.
“For this effort, we verified and started to scale up a process that had already been developed by ARL,” said Schmidt.
Additionally, the Solvus Global team integrated their APEX manufacturing intelligence software with VRC Metals’ GEN IV® High-Pressure Cold Spray System.
“APEX receives data from the GEN IV® system and leverages machine learning to optimize cold spray processes,” said Schmidt.
“The APEX software is a machine learning tool and also a production process and management tool,” said Richards. “APEX is designed to capture KPIs from the process itself to ensure that process performance can be routinely tracked as a function of the critical process variables. It’s basically a bolt on software tool to allow for enhanced production control.”
The Boeing team identified the CH-47 Chinook engineering requirements and testing data required to validate the material for use with the selected component, and worked closely with the DOD customer to approve the qualification test plan. Boeing tested cold spray powder and process improvements under development, designed and manufactured fabrication tooling for the rotor blade erosion guards, and performed lab evaluations of part specimens. Boeing is working closely with ARL and the project partners to perform trials to determine optimal tooling release methodology and surface finishing and will help integrate a sensing system with the GEN IV® cold spray system for monitoring powder feed rate in real time.
“Rotor blade design and maintenance must address a large number of requirements to satisfy safety and quality while proving to be cost-effective and timely for the warfighter,” said Ken Young, Associate Technical Fellow, Materials & Processes – Boeing Vertical Lift. “Rotor blades are extremely complicated structures that have a combination of different material types. The component we’re working on for the repair technology must protect the composite structure underneath and must be able to survive very severe environments with sand and rain erosion, along with other types of impacts.”
The Boeing team started by identifying all the aircraft and component requirements, then determining all the test data that needed to be generated to show that the new component and repair processes are at least as good as the existing repair system.
“We worked very closely with the DOD customer. It was extremely important to get them involved early in the process,” said Young.
After the DOD approved the qualification test plan, the Boeing team began the complex testing process.
“We worked closely with ARL and the other project partners to develop the powder and the cold spray deposition technology,” said Young. “ARL sent cold spray deposited Niobium, and we fabricated test coupons from that material to test in static and fatigue environments. We also focused on verifying how the metal protection is bonded onto the rotor blades.”
“The erosion guards are sprayed onto what we call a mandrel, which is a hard metal piece that has the same shape as the rotor blade,” said Ellingsen. “Once the guard has been sprayed, we release it from that mandrel, and then it will be adhesively bonded onto the rotor blade on the aircraft.”
Working closely with ARL, the Boeing team identified Chinook blades to use as qualification articles. They will use Chinook blade articles, install the prototype components, inspect the component installations, and perform track and balance testing, along with sand and rain erosion testing, to make sure all requirements are met.
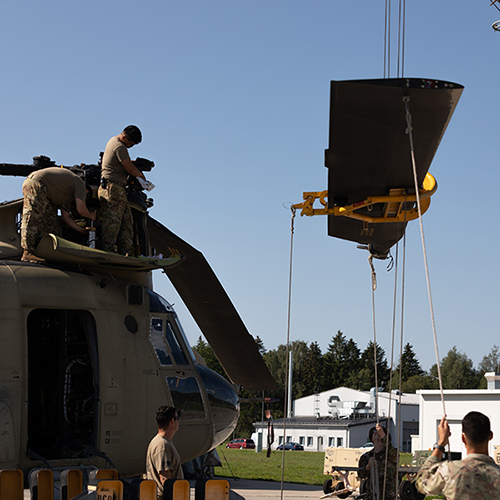
“Our development testing has already showed that both the Niobium and the adhesive system can survive in harsh, extreme-temperature environments,” said Young. “Currently, cold spray additive manufacturing is competing with electroformed Nickel. The cold spray additive manufacturing process we developed in this project to produce erosion guards has been shown to be a more erosion-resistant material than electroformed Nickel. Cold spray additive manufacturing is a near-net process and enables the manufacturing of erosion guards more efficiently.”
In March, the team integrated the Siemens Energy component with the GEN IV® High-Pressure Cold Spray
System and helium recovery system. The team spent several weeks conducting a final acceptance test, to make sure that the system worked as intended.
“The cell that Siemens Energy integrated with the GEN IV® system is the pinnacle achievement of demonstrating that we can create a system with a very high degree of complexity to manufacture these unique components,” said Richards. “To my knowledge, this project developed the first airworthy cold spray AM part for a highly complicated shape.”
The project will have a broad impact across an entire class of platforms. Although the team started with the Chinook, other Army helicopters will benefit from this technology.
“While erosion guards for different helicopters will require different geometries, fundamentally you can use the same material and manufacturing technology for all of them,” said Richards.
Currently the project is moving into another phase focused on making the powder more robust.
“In aerospace, establishing a controlled and consistent process is extremely important, and for this work that starts with the powder,” said Young. “We’re working closely with our partners to establish a consistent process for each step of this work.”
All project partners remarked on the team’s effective collaboration on an extremely complex project.
“We worked well as a team,” said DeAscanis. “We designed a new system and made it as small as it could be so that it’s efficient when it comes to running it, because it uses helium, which is expensive. We went with a very small design so it can operate as cost effectively as possible.”
Young reflected on the overall value of the project: “Rotor blades are expensive to both maintain and to replace. This repair process will ultimately make rotor blades last longer, reducing maintenance costs.”
Ellingsen commented on the public benefit of the work done on this project: “These erosion guards will provide a safety improvement not just for military aircraft, but also for civilian helicopters and propeller aircraft.”