A growing number of DOD maintainers will no longer have to rely on outdated maintenance procedures, two-dimensional drawings, and legacy data collection methods. A recent CTMA project has established a new, state-of-the-art digital platform—called the Redesigned Platform Repair Process (RPRP)—for maintaining and collecting data on military systems. This platform provides maintainers with interactive 3D models, along with AR/VR capabilities to support virtual simulations that enable personnel to interact with a digital twin for training and real-time repairs.
This project brings together the Office of Naval Research (ONR) and capabilities from multiple industry partners. The RPRP solution combines four software technologies—PHM Technology’s Maintenance Aware Design Ecosystem (MADE), Edlore’s AR/VR tools, Siemens Digital Industries’ Teamcenter, and Mendix’s Studio Pro—to create an advanced digital platform for managing and maintaining military systems.
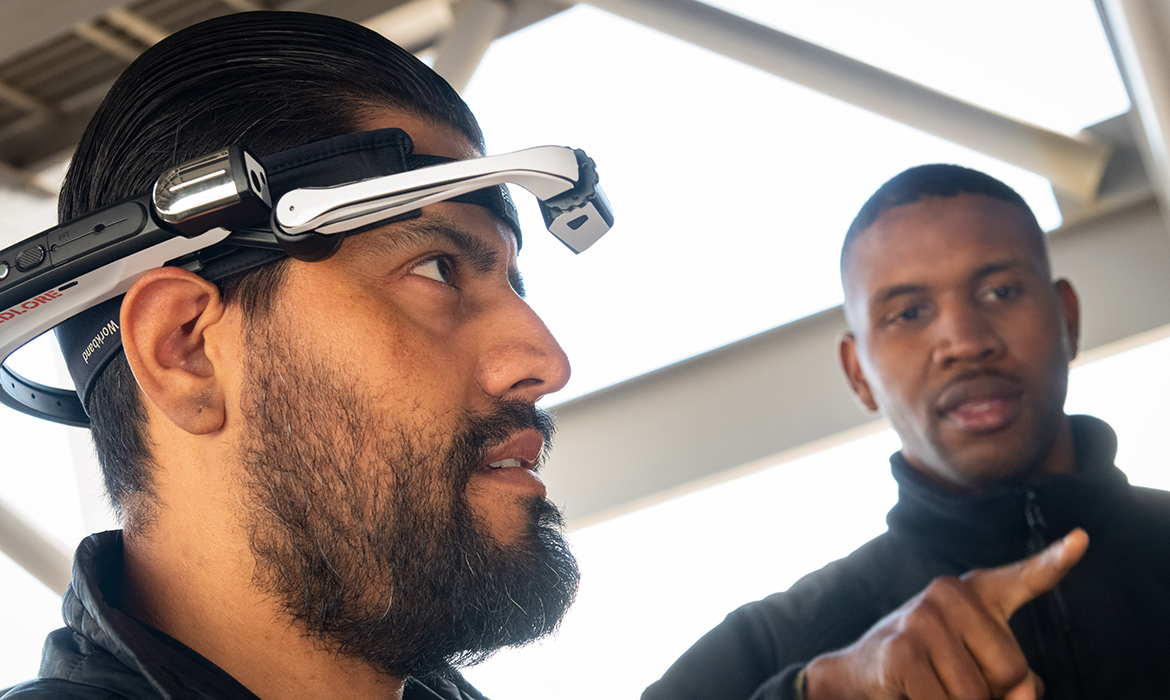
“This project is far reaching but at the same time has practical applications to the military logistics community,” said Peter DeSalva, an Office of Naval Research (ONR) Support Contractor, Subject Matter Expert, and Senior Advisor for Peraton, a national security and technology firm. “We wanted to reduce the amount of maintenance effort that’s required by changing the platform designs incrementally. To do this, we had to understand what activities are currently used to maintain platforms. We wanted to gather the data to figure out where we would get the most return on design changes. We decided to use virtual reality and digital twins to create a duplicate of a particular platform, or a component of the platform, to capture the activities that go into keeping that component up and running.”
The RPRP platform is a digital ecosystem that works in the following way. Edlore software, a mobile work order management solution, takes the technical orders and maintenance procedures and transforms them into interactive 3D models. These models are integrated into the RPRP platform to allow for visual, step-by-step maintenance tasks. Edlore also incorporates AR/VR capabilities to support virtual simulations, enabling personnel to interact with a digital twin for training or real-time repairs.
Siemens’ Teamcenter, a product life-cycle management software, serves as the backbone, centralizing design and maintenance data. It manages the product life cycle, including engineering data, bills of materials (BoM), and technical documentation. Teamcenter synchronizes these data with the digital twin models of the physical systems.
The MADE data modeling software provides detailed analytical insights, including failure mode effects analysis (FMEA) and reliability-centered maintenance (RCM) strategy. It monitors the health of systems, predicts maintenance needs, and identifies potential system failures before they occur, feeding this data back into the platform for proactive, rather than reactive, maintenance.
The Mendix software serves as the user interface layer, allowing users to easily interact with the system through a low-code/no-code interface. Mendix connects the analytical insights from MADE, the lifecycle data from Teamcenter, and the visual models from Edlore to present users with an intuitive dashboard for managing maintenance workflows, reviewing tasks, and monitoring system performance in real time.
The project focused on one vehicle: the Joint Light Tactical Vehicle (JLTV) and specifically addressed the challenge of maintaining line replaceable units (LRUs), essential support items that are removed and replaced at field level to restore an end item to an operationally ready condition. LRUs require efficient management and replacement to ensure operational effectiveness in harsh environments.
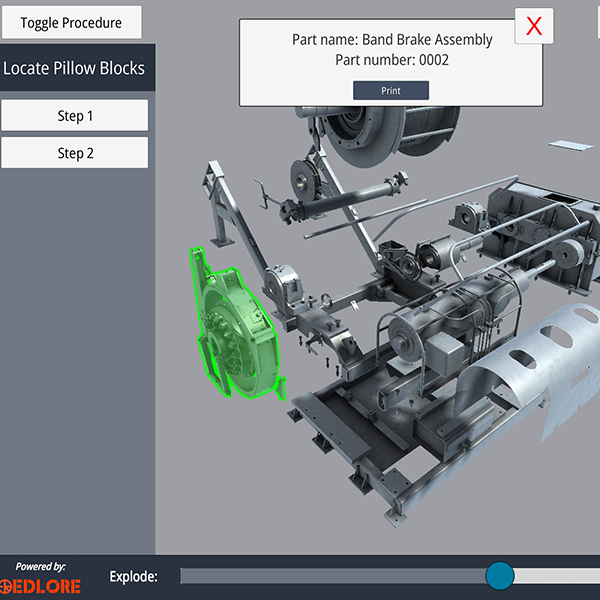
“For this project, we looked at the JLTV, specifically the 3D renderings of one of the drive components, to show how it is put together and how it operates,” said DeSalva. “What is impressive to me is how quickly the team was able to take some very basic two-dimensional drawings and turn them into 3D renderings. These can be applied anywhere there is an expectation of performing maintenance activities, ranging from a truck driver who doesn’t have a mechanic with him but has to execute a mechanic-type task in order to get his vehicle back up and running, to the very highly trained mechanic back at the Marine Corps Logistics Base Albany where they’re doing major overhauls of entire fleets of vehicles, and everything in between.”
Along with 3D visualizations, maintenance personnel can visualize repair tasks with virtual replicas (digital twins) of equipment using AR/VR. The use of these visualizations in training and task execution helps to minimize human errors, enhancing safety and reducing the need for corrective maintenance.
The RPRP platform also combines historical and real-time data on maintenance actions to facilitate predictive maintenance and actionable insights for repair teams. The rapid identification of issues ensures immediate repairs and/or replacements to reduce maintenance cycle times and enhance mission readiness.
Because the RPRP platform is cloud-based and adaptable, it can be utilized for many different military systems, from ground vehicles to aircraft. The platform is scalable across the DOD to support warfighters’ sustainment of assets in the field.
DeSalva reflected on the benefits of the RPRP platform: “I spent 30 years in the Marine Corps, first as an infantry officer, then 20 years as a logistician. When warfighters operate inside the likely enemy combatants’ long-range fires, they’re not going to have continuous support. They’re going to have at best intermittent support, and any support they have may be interdicted and eliminated before it gets to them. I know this kind of technology will be very beneficial to folks in the field.”
The long-term objective of the project is to collect data on sustainment activities to make military platforms more robust, longer lasting, and require less maintenance.
“If we simplify the designs, it will be easier to keep platforms maintained and make them more reliable,”
said DeSalva.
Beyond the DOD, the RPRP platform has numerous potential public benefits, as it can be adapted for use in multiple commercial industries including oil and gas, mining, manufacturing, and transportation.